Guide to safe use of work equipment
By Alan Boswell Group
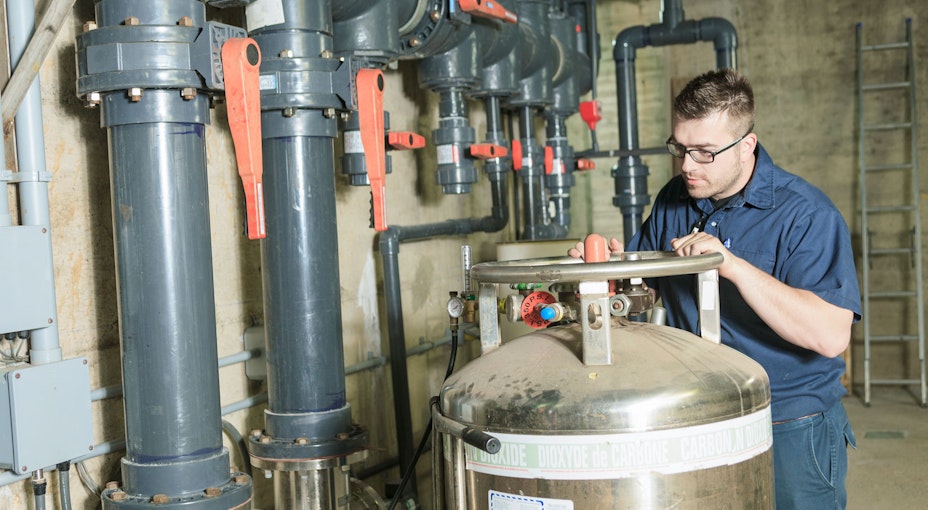
Definition
Work equipment is any machinery, appliance, apparatus, tool, or installation for use at work (whether exclusively or not). This includes equipment which employees provide for their own use at work. The scope of work equipment is therefore extremely wide.
The use of work equipment is also very widely interpreted and ‘…means any activity involving work equipment and includes starting, stopping, programming, setting, transporting, repairing, modifying, maintaining, servicing and cleaning.’
Source: HSE
Regulations
PUWER is the baseline where regulation starts. LOLER, PSSR, and other health and safety regulations such as COSHH (Control of Substances Hazardous to Health) and PPE (Personal Protective Equipment) are in addition to this. These regulations are explored further in the rest of this document.
PUWER - Provision and Use of Work Equipment Regulation
Applies to all work equipment. The object of the regulation is to ensure that the working life of everyone who uses or comes into contact with work equipment or machinery remains safe.
Select and provide the right equipment for the job
Does it have the correct guarantee of safety?
Do any additional hardware or software measures need to be imposed?
Ensure work equipment is safely used by trained people
Training should be undertaken at the expense of the company and in company time
Training should be recorded for future reference
Inspect and maintain work equipment so it remains safe
Risk assessments should be suitable and sufficient
Risk assessments should be an examination of what can cause harm
How often does a risk assessment need to be carried out?
These should be carried out every 12 months – or sooner if a process or a piece of machinery changes.
Risk assessments are not about providing reams and reams of paperwork, but a list of sensible measures to control the risk presented.
HINTS
Having a CE mark does not guarantee equipment safety.
Hardware measure – a fixed guard to keep body parts away from moving machinery while it’s in operation. Software measure – a safe system of work or a risk assessment.
LOLER - Lifting Operations and Lifting Equipment Regulations
Regulation applies to organisations and businesses where their employees lift or lower loads – an equipment’s primary function is for lifting.
The regulation requires that:
All equipment used for lifting is fit for purpose
Is appropriate for the task
Is suitably marked
Must display a Safe Working Load – this is statutory
Is subject to statutory periodic ‘thorough examination’
Must be undertaken by a competent person who has theoretical knowledge and experience
Must be inspected every 6-12 months. The frequency will be determined by the competent person carrying out the inspections.
What is the difference between a service and a thorough examination?
A service can be carried out by a maintenance engineer who might change oil or tyres e.g. like a car service at a garage. A thorough examination must be carried out by a competent person who has the knowledge and experience to be able to detect defects e.g. like an MOT – it’s a statutory legal requirement.
So, you do need to check your documents because they are not the same thing?
A service provider carries out a service, not a LOLER inspection. A LOLER inspection should not be carried out on an individual’s own maintenance work.
PSSR - Pressure Systems Safety Regulations
Covers the safe design and use of pressure systems aiming to prevent serious injury from the hazard of stored energy (pressure) as a result of the failure of a pressure system or one of its component parts. Source HSE
Checks must be carried out by a competent person
250 bar litres or more requires a statutory inspection
Less than 250 requires an inspection under PUWER
Pipework of a pressure system checks
Half a bar (roughly 7psi) or more should be inspected and requires a written scheme of examination drawn up by a competent person who will tell you the frequencies and the type of inspection/examination required.
How do you find out if your system needs checking under the regulations?
Somewhere on the equipment will state its safe working pressure and capacity in litres –then multiply the two together.
What is a written scheme of examination?
It determines the frequency and the nature of the examination and is drawn up by a competent person. It will define what exactly needs an examination; what safety valves should be tested; the internals of a vessel; how often, and if there is any other pipework or anything else that requires an inspection.
HINT
Defined in the written scheme of examination, frequencies:
Equipment such as the coffee machine with steam – 14 months
Air systems that are working – 12-13 months with a working thorough examination every 24-26 months
Any other gases – 5-10 years
LEV - Local Exhaust Ventilation
Effective LEV or dust/fume extraction can carry away airborne contaminants before they can be breathed in. Source: HSE
COSHH Regulations – Control of substances hazardous to health and PPE – Personal Protective Equipment
Under these regulations, it’s a legal duty to use engineering control measures to remove or control airborne contaminants in a workroom.
Statutory inspections should be undertaken by a competent person/engineering surveyor and carried out at intervals according to the hazardous substance being extracted.
The regulations contain a hierarchy of control which is a legal requirement to follow. The use of PPE is a last resort, all other measures in terms of making sure you can’t eliminate the substance; substitute it with something less harmful or by using engineering controls/isolating use of the substance must be considered before the use of PPE.
What happens if employees refuse to wear PPE?
An organisation must investigate why they are refusing to use the PPE – it might be uncomfortable, it might make working with the hazardous substances more difficult or more dangerous, so have those discussions first. Everyone’s different, everyone’s face and body is different so products to suit the individual need to be found. However after that exercise, if the individual is still refusing to wear the PPE it is important to go down the disciplinary route. The employer may be liable for non-use of PPE where employees are exposed to hazardous substances.
Summary
This guidance document has highlighted some of the regulations that govern the use and supply of work equipment and how they interlink. PUWER is the baseline regulation – some work equipment will be regulated through other health and safety legislation e.g LOLER, PSSR and COSHH (LEV).
Points to remember:
Provide the right equipment for the right job
Adequately train your employees
Inspect and maintain the equipment properly
Supply risk assessments and safe systems at work
Need help with your risk management?
To find out more about risk management and health and safety consultation for your business, speak to our team.